This study evaluates biorefinery bio-oil feedstock costs at the plant gate for a prospective field pennycress (Thlaspi arvense L.) to sustainable aviation fuel (SAF) supply chain. The biorefinery would supply SAF to the Nashville, Tennessee international airport. Supply chain activities include pennycress production, transporting oilseed to a crushing facility, processing of oilseed into bio-oil, and transporting bio-oil to the biorefinery. The ASCENT Techno Economic Assessment (TEA) for a HEFA biorefinery required 260,706 Mg per year of bio-oil to produce 162 million liters of SAF, 71.46 million liters of diesel, 24.17 million liters of naphtha, 31.6 million liters of LPG, and 22.12 million liters of propane.
- Tanzil, A.; Brandt, K.; Zhang, X.;Wolcott, M.; Garcia-Perez, M. A Review of Alternative Jet Fuel Technologies: Comparison of Technoeconomic and Environmental Performance with Standardized Criteria. Unpublished work, 2019.
- The study citation: Trejo-Pech, C., J. A. Larson, B. C. English, and T. E. Yu. 2019. Cost and Profitability Analysis of a Prospective Pennycress to Sustainable Aviation Fuel Supply Chain in Southern USA. Energies, 12, no. 16: 3055.
Potential Crush Facilities
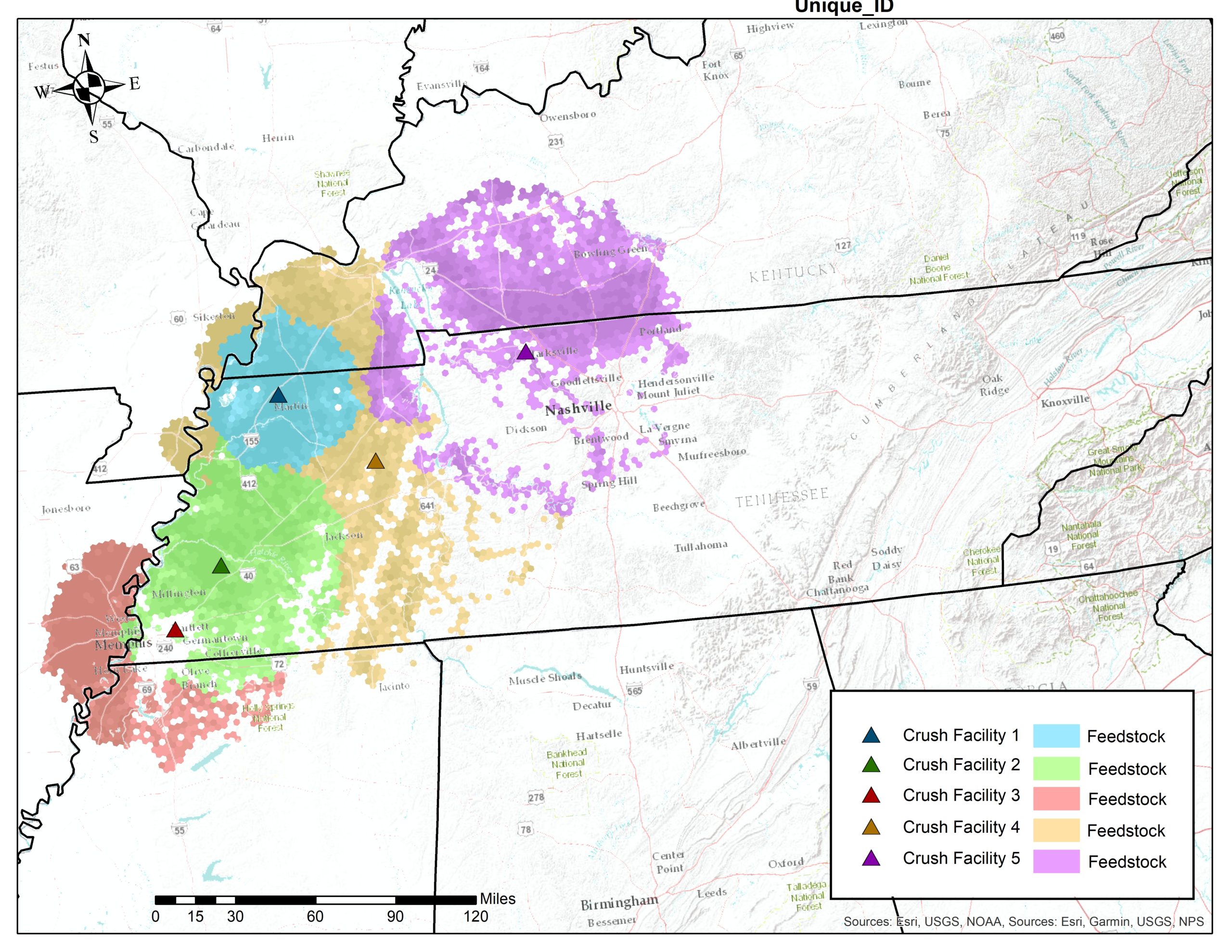
Tennessee can support five pennycress crush facilities operating at 800 tons per day, 328 days per year.
Pennycress is produced as a cover crop between corn and soybeans.
Number of facilities are limited by corn and soybean acreage currently in production.
Nashville Airport Demand
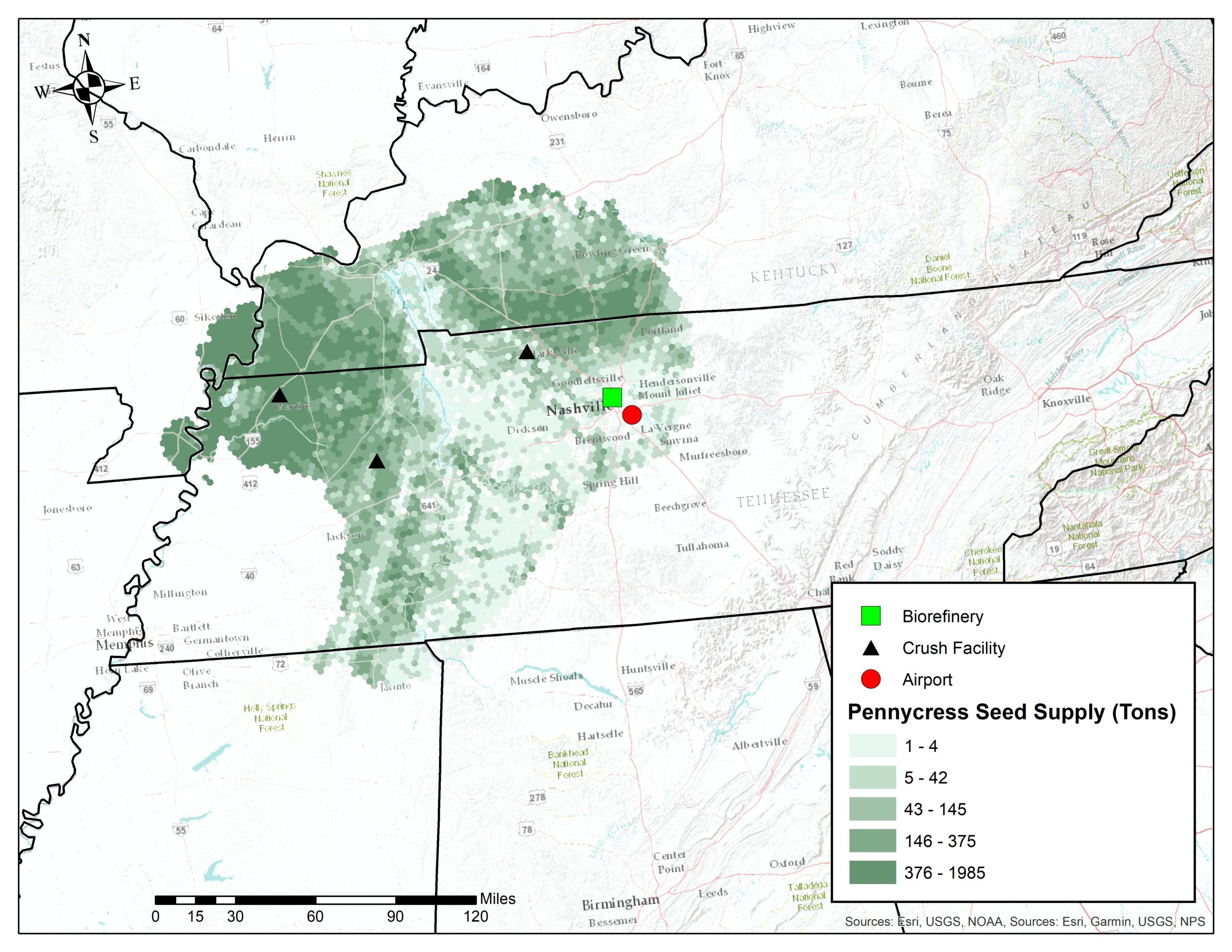
Three crush facilities are required to supply Nashville airport demand
The crush facilities are located at
- Union City, TN
- Clarksville, TN
- Huntington, TN
Total Feedstock Cost Delivered to Crush Facilities $115.7 million
Average per ton-mile distance from field to crush facility is 44 miles each ton of seed travels.
Crush Facilities Cost of Feedstock
Location | Farm Gate Cost a | Transportation Cost Field to Crush | Total Delivered Cost | Cost per pound |
---|---|---|---|---|
Crush Facility 1: Union City | $56,991,002 | $1,245,356 | $58,236,358 | $0.088 |
Crush Facility 4: Clarksville | $56,068,534 | $2,468,940 | $58,537,473 | $0.090 |
Crush Facility 5: Huntingdon | $56,429,483 | $3,464,951 | $59,894,434 | $0.092 |
a Cost of Pennycress at $172.80/acre
Delivered Feedstock Cost to Biorefinery: Allocation among principle activities
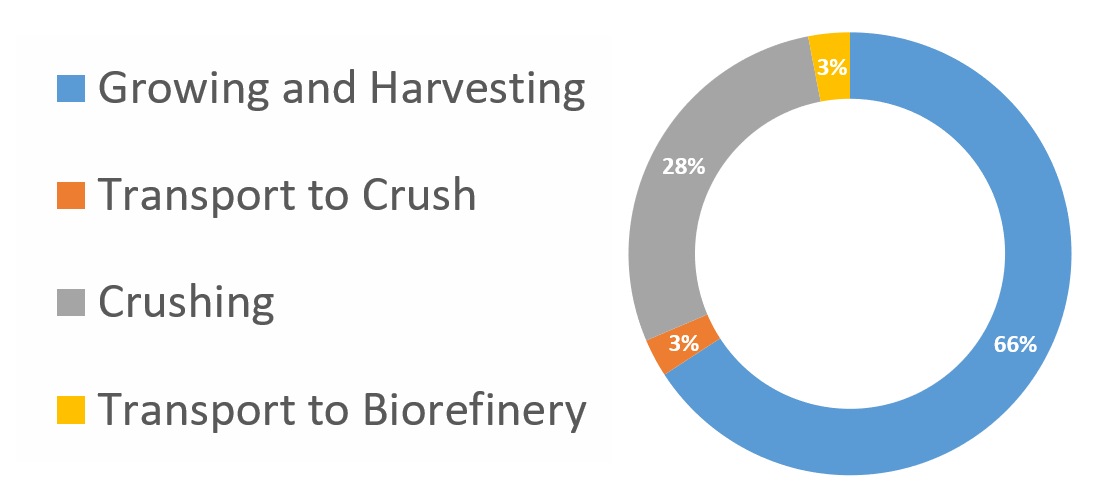
Supply Chain Cost:
Two pennycress farm gate prices
– $0.081 and $0.108 per pound
Supply Chain Event | Covers Expenses of Pennycrest ($0.081) | Uses Farmgate Price of ($0.108) |
---|---|---|
Growing and harvesting | $108,539,669 | $169,489,019 |
Transport to Crush | $7,179,247 | $7,179,247 |
Crushing | $73,045,677 | $73,045,677 |
Transport to biorefinery | $7,815,459 | $7,815,459 |
Biorefining a | $44,900,000 | $44,900,000 |
Transport to airport | $1,152,444 | $1,152,444 |
Total | $242,632,495 | $303,581,845 |
a Source: Costs taken from Tanzil, A.; Brandt, K.; Zhang, X.;Wolcott, M.; Garcia-Perez, M. A Review of Alternative Jet Fuel Technologies: Comparison of Technoeconomic and Environmental Performance with Standardized Criteria. Unpublished work, 2019.
Final Comments
The ASCENT HEFA to SAF TEA purchases feedstock (oil) at $1.03 per kg.
The Economic analysis demonstrates that the pennycress oil could be available at that price or lower. We found the value ranges from $0.80 to 1.09 per kg depending on whether the crush facility paid $0.081 to $0.108 per pound.
The analysis assumes a 12.2% return on investment for both the crush facility and the biorefinery.
Table 7. Estimated supply chain costs from field to biorefinery
Supply Chain Events | Covers Expenses of Pennycrest ($0.081/lb) | Uses Price at Crush Facility ($0.108/lb) |
---|---|---|
Volume Delivered to Biorefinery (tons/year) | 287,300 | 287,300 |
Delivered Cost per pound | $0.38 | $0.49 |
Delivered Cost per kg | $0.83 | $1.09 |
Difference between our calculation and ASCENT HEFA TEA of $1.03/kg | $0.20 | -$0.06 |